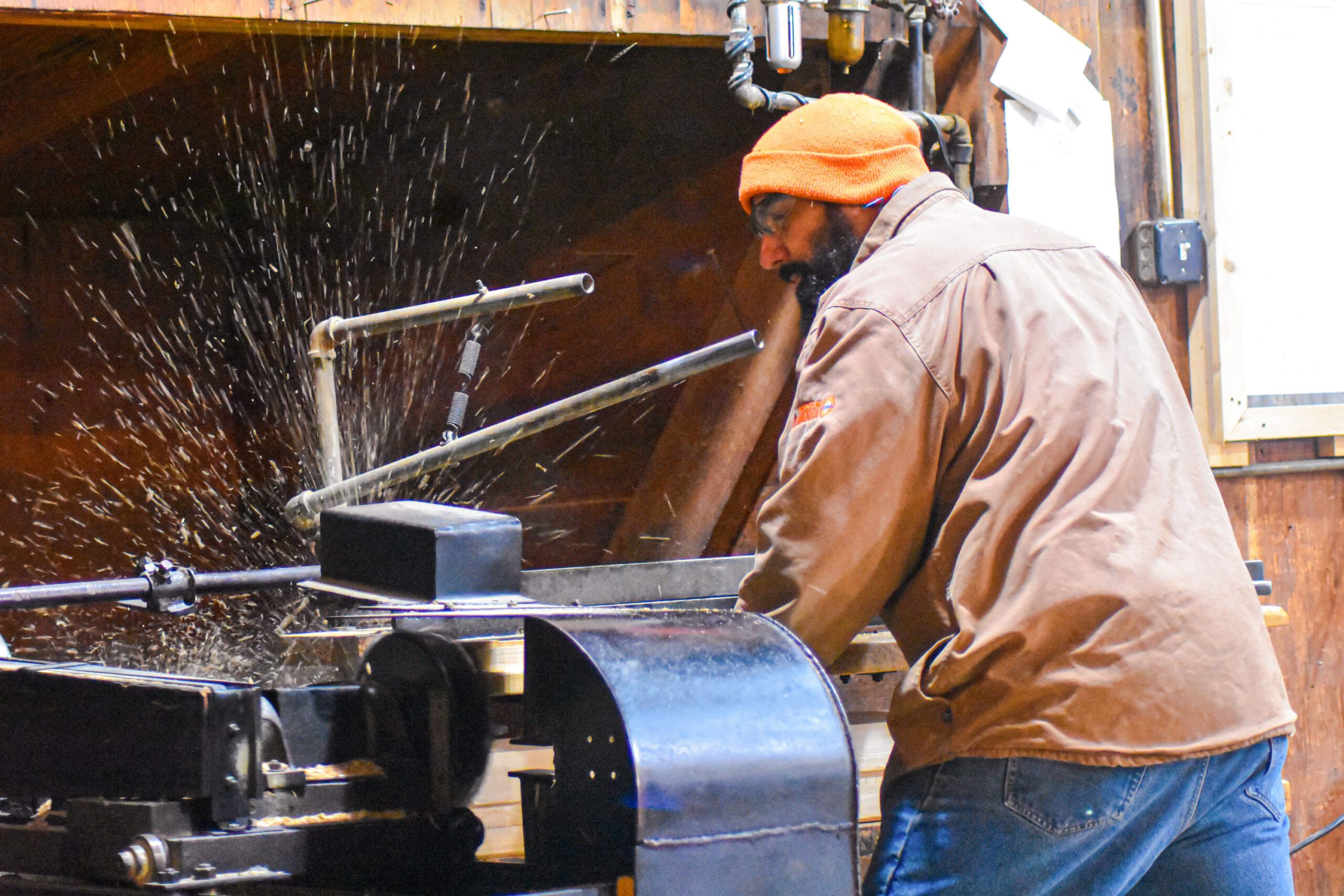
HOULTON, Maine — In 1923, Bruce Ward was selling cedar poles to a northern Maine telephone company. As his pile of leftover logs grew, Ward hand-built himself a home with the surplus poles.
And before long, as word spread about his cedar log home, Ward was inundated with requests for him to build more. That’s when he built his first log cabin for sale.
Now, 100 years later, Ward Cedar Log Homes still follows the hands-on lead of its founder by milling and cutting cedar in their Houlton facility.

Bruce Ward started Ward Log Homes in 1923 after he made a log home for himself from cedar telephone poles. Today, Ward Cedar Log Homes is still making cedar cabins and home in Houlton. (Courtesy of Ward Cedar Log Homes)
Only after all log and wood cuts have been checked and rechecked are the home kits packaged and shipped out to U.S. and international locations like Japan, the Dominican Republic, South Korea, Canada, Taiwan and the Philippines, Director of Sales and Marketing Ron Silliboy said.
“Each log is handled three to four times,” he said.
Even when other log companies started popping up and began automating the process, Ward log homes chose to stick with their hand-on approach while discovering their own milling and wood cutting innovations instead.
“Our cedar logs are naturally rot- and pest-resistant and proven to be eight times more insulating than brick and 21 times more so than concrete,” Silliboy said adding that white cedar logs are the cornerstone of the company..
In the 1930s, Bruce Ward developed a milling technique with interlocking corners that they still use on all of their log cabins and homes. The company also pioneered pre-cutting and numbering logs in the factory to make on-site construction easier.

Craig Tweedie and Mike Doughty (cutting) prepare cedar logs for new home packages for Ward Cedar Log Homes in Houlton. )Kathleen Phalen Tomaselli | Houlton Pioneer Times)
In the 1970s and ’80s the company developed a more milled finish for the previously rough hewn logs. By the 1980s and ’90s they tweaked their patented exterior caulking groove for added air-tightness and efficiency, Silliboy said.
At the company’s manufacturing facility near the Houlton Airport, logs and cedar boards are stacked on pallets. The scent of fresh cut cedar fills the open spaces as employees cut grooves into logs that will later be used for caulking when the home is built.
Staff debark logs and then spin them in a machine that whittles the log or post to the specified dimension. Employee Chuck Grim checks the cuts before placing the home pieces in a section ready for shipping.
“It’s up to me to make sure everything is right,” Grim said last week while stacking inspected home pieces.
One average-sized log home package costs about $125,000 and it takes two flat-bed trailers to ship the materials to a customer, Silliboy said. The company also supplies a 110-page instruction manual with the home kits to help builders or the customer assemble their new log home.
“We must be attentive to the customer and make sure we deliver what they want,” he added.

Charles Grim (rear) and Charles Long trim a cedar post to fit the required dimensions for Ward Cedar Log Homes in Houlton. (Kathleen Phalen Tomaselli | Houlton Pioneer Times)
The company name has been tweaked with new ownership. In the 1950s it was Ward Cabin Company. In the 1980s it became Ward Log Homes, and starting in the 1990s, the name changed to Ward Cedar Log Homes.
Ward Cedar Log Homes has 14 employees, most with decades of longevity. Controller Mike Doody has been with the company for nearly half of its existence, Silliboy said.
New this year, Ward is doing away with felt paper for roofs, switching to a synthetic roofing underlayment. This will offer better protection, he said.
Their key to a successful 100 years in business has been a commitment to excellence and quality, and the people who work for the company are an important part of their success, Silliboy said.
As far as what the company wants to see for the future, Silliboy was definite: to be in business for another 100 years, he said.